Embracing Lean Six Sigma Green Belt Projects: A Catalyst for Organizational Transformation and Cost Savings
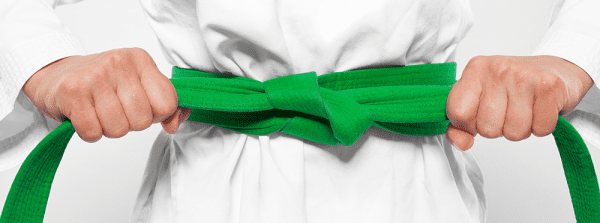
By Oscar Cuellar- Program Director, Corporate Training and Executive Education
In today’s fiercely competitive business environment, organizations are constantly seeking ways to enhance efficiency, reduce waste, and improve quality. Lean Six Sigma, a methodology that combines the waste-reducing principles of Lean with the quality improvement tools of Six Sigma, has emerged as a powerful framework to achieve these goals. Among its various levels of certification, the Green Belt represents a critical level where employees gain a foundational understanding of these methodologies, enabling them to lead small-scale projects and contribute significantly to larger initiatives. While the Lean Six Sigma Green Belt projects can provide immediate cost savings, to sustain those cost savings, organizations must fully embrace the concepts of Lean Six Sigma by providing a supporting cast of White and Yellow Belts (I call them the worker bees) and Orange Belts (senior management champions who clear obstacles). A Green Belt project leader alone without this supporting cast will almost certainly become a One-and-Done project leader with a paper certification that only looks good on a resume or LinkedIn profile and I want to discuss the importance and benefits of Lean Six Sigma, not only to its customers but also to the organization, to prevent the One-and-Done effect.
The Benefits of Lean Six Sigma Green Belt Projects
1. Improved Process Efficiency and Quality
Lean Six Sigma Green Belt projects focus on identifying and eliminating waste, reducing process variation, and improving quality. By utilizing tools such as DMADV (Define, Measure, Analyze, Design, Validate) or DMAIC (Define, Measure, Analyze, Improve, Control), employees can systematically address inefficiencies and defects. The results are often tangible: reduced cycle times, lower error rates, and higher customer satisfaction. For instance, a manufacturing company might use a Green Belt project to streamline its production line, thereby reducing defects and lead times and improving product quality.
2. Cost Savings
One of the most compelling benefits of Lean Six Sigma Green Belt projects is waste reduction and cost savings. By eliminating inefficiencies and waste, organizations can significantly cut costs. For example, in a healthcare setting, a Green Belt project might focus on reducing the time patients spend waiting for services. By optimizing this process, the organization not only improves patient satisfaction but also reduces operational costs. These cost savings can then be reinvested into other areas of the business, fostering growth and innovation.
3. Employee Development and Engagement
Green Belt projects provide employees with valuable skills and knowledge. They learn to use data-driven analysis to solve problems, which enhances their decision-making capabilities. Moreover, being involved in these projects can boost employee morale and engagement, as they see the direct impact of their efforts on the organization’s success. This empowerment can lead to a more motivated and innovative workforce, which is crucial for long-term success.
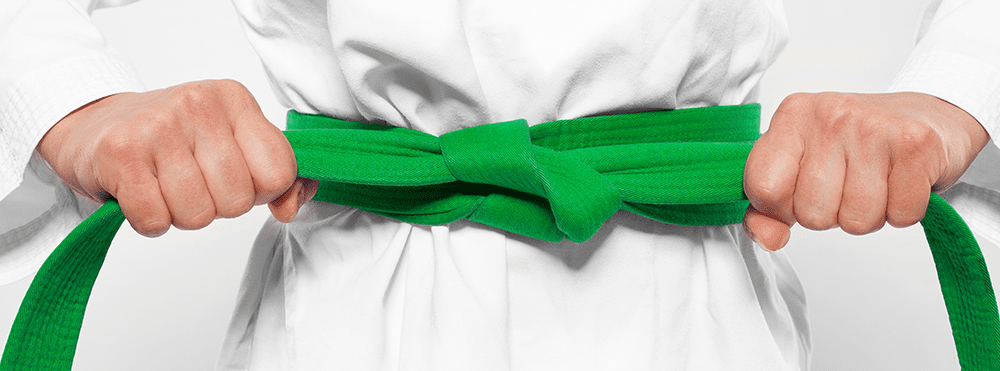
4. Enhanced Customer Satisfaction
Lean Six Sigma Green Belt projects often focus on improving processes that directly affect the customer experience or end-user products. By ensuring that products and services meet high-quality standards and are delivered in a timely manner, organizations can enhance customer satisfaction and loyalty. In turn, this can lead to repeat business, positive word-of-mouth, and a stronger market position.
5. Foundation for Continuous Improvement
Green Belt projects lay the groundwork for a culture of continuous improvement. Employees trained in Lean Six Sigma principles are equipped to identify opportunities for improvement on an ongoing basis. This proactive approach ensures that the organization continually evolves and adapts to changing market conditions, technological advancements, and customer needs.
The Importance of Organizational Support for Lean Six Sigma
While the benefits of Lean Six Sigma Green Belt projects can be substantial, realizing and sustaining these benefits requires more than just training the Green Belt employees. It necessitates a fundamental cultural shift within the organization. Through my own experience, I have learned that for Lean Six Sigma to truly thrive, an organization must fully support and embrace this change. Otherwise, the training will be completed, certificates awarded, and no further efforts will be made.
1. Leadership Commitment
The success of Lean Six Sigma initiatives hinges on strong leadership commitment and engagement. Leaders must not only endorse these projects but also actively participate, provide the necessary resources, and clear any obstacles that the Green Belt may encounter. This includes the allocating of resources and time for employees to work on Green Belt projects, investing in training, and recognizing and rewarding successes. Leadership commitment is best provided when leaders themselves undergo Orange Belt training to learn how to identify, track, and support Green Belt projects. When leaders demonstrate their commitment, it sends a powerful message throughout the organization that Lean Six Sigma is a priority and is here to stay.
2. Creating a Supportive Environment
For Lean Six Sigma to be truly effective and long-lasting, organizations must create an environment that supports experimentation and learning. This involves fostering open communication, encouraging collaboration across departments, and being willing to take calculated risks. Employees should feel safe to identify problems and suggest improvements without fear of reprisal. Additionally, any project failures should not be viewed as a negative but as a learning point for future projects. A supportive environment creates a culture where continuous improvement becomes ingrained in the organization’s DNA.
3. Aligning Lean Six Sigma with Strategic Goals
To maximize the impact of Lean Six Sigma Green Belt projects, it is essential to align them with the organization’s strategic goals. This ensures that the projects contribute to the broader objectives and priorities of the business. For instance, if an organization’s strategic goal is to enhance customer satisfaction, Green Belt projects should focus on areas that directly affect the customer experience. The Orange Belt (senior leadership) has the pre-work of collecting the Green Belt project ideas and ensuring they align with the organization’s strategic goals. This alignment creates synergy and amplifies the benefits of Lean Six Sigma.
4. Investing in Training and Development
Sustaining a culture of Lean Six Sigma requires ongoing investment in training and development. Organizations should provide continuous learning opportunities for employees at all levels, from White and Yellow Belts (team members), to Green Belts (team leaders), to Black Belts (organizational leaders), to Orange Belts (senior leaders/champions), and beyond. This not only keeps skills current but also helps to build a robust pipeline of Lean Six Sigma practitioners who can drive improvement initiatives across the organization.
5. Measuring and Celebrating Success
Finally, it is crucial to measure the impact of Lean Six Sigma Green Belt projects and celebrate successes. Even failed projects provide data and learning points that can be utilized in planning and implementing future Green Belt projects. By tracking key performance indicators and showcasing successful projects, organizations can demonstrate the tangible and financial benefits of Lean Six Sigma. Celebrating successes not only reinforces the value of these initiatives but also motivates employees to continue their improvement efforts.
Conclusion
Lean Six Sigma Green Belt projects can offer a myriad of benefits, from improved process efficiency and cost savings to enhanced customer satisfaction and employee engagement. However, to truly reap these benefits, an organization must fully support the cultural change required by Lean Six Sigma. This means committing to leadership involvement, creating a supportive environment, aligning projects with strategic goals, investing in ongoing training, and celebrating successes. Through my journey with Lean Six Sigma, I have seen firsthand that when an organization wholeheartedly embraces this methodology, it can unlock remarkable potential and drive sustained success. I have also experienced the frustrations when an organization doesn’t fully embrace the change and only pays lip service to that one individual’s professional development and abandons the change because “it’s too hard”.
As organizations navigate the complexities of today’s business landscape, Lean Six Sigma Green Belt projects can serve as a powerful catalyst for transformation, enabling them to achieve excellence and maintain a competitive edge. Embrace the change and reap the benefits or fight the change and stagnate.
If you’d like to learn more about our Lean Six Sigma programs, please email me at ocuellar@charlotte.edu to set a time for a quick conversation, or check out our Course Catalog for a program description.